alex00
Well-known member
I wanted to give a special "Thank You!" to Al, (DesertThumper) for all his help with this install. He was able to answer all my questions having already done this.
I picked up the Viair Constant Duty air system (part 10007) to use with airbags, and general airing up duty. I installed it this weekend in my 2014 Ram 3500. Hopefully my pictures can help the next person attempting this install.
I started by determining the best location for the tank and compressor. I found a spot on the passenger side, under the bed, between the duals and the running board.
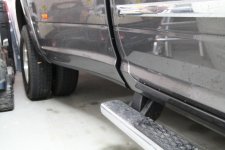
The front of the truck is to the left in this photo, I'm on my back, looking straight up. The forward rear spring hanger is just shadowed in this picture. This is the underside of the bed. There are two M12 x 1.75 threaded holes on frame of the bed. They are spaced about 19" apart.
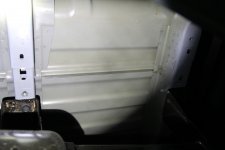
After measuring for the bolt holes, I test fit the plate. The plate measured 10" x 22" with a 3" square cut out of the corner to clear a frame member.
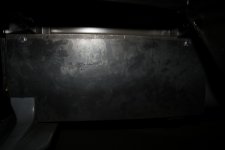
This is the orientation of the tank and compressor on the plate. Once mounted they hang upside down, with the tank on the outboard side.
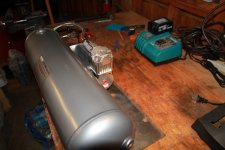
I lucked out with the remote air intake for the compressor. There was a hole already in the sheet metal, between the inner and outer bed skin. This photo is looking forward, inside the passenger side dual fender.
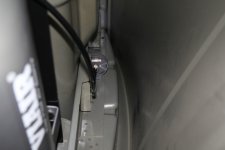
The scariest part of the install was ripping up the carpet and removing the glove boxes. The carpet pulls away easily from the outboard forward corner. It tucks back into place easily, too. I pulled the carpet far enough down to expose the bottom of the thick carpet pad. The lower glove box comes out easily, pull the sides in and tip it forward. There is a little spring loaded string that unhooks from the outboard side of the glove box. The upper glove box has a single screw holding it in on the back. Once removed the liner pops out by pushing it from the back. There are several clips around the perimeter holding it in place. One of these will pop as you push from behind. Unplug the light wire and it is all free.
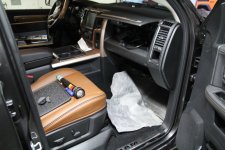
Once I had the carpet pad exposed, I lifted it to access the oval plastic cover. There are several of these covers, but this one is on the slanted portion of the passenger foot well. I wasn't sure how to get it off, but Al assured me it came off with a screwdriver. Sure enough, it pops up, and reveals a very nice hole for getting airlines into the cab. I routed the airlines behind the plastic panel to the right, and up behind the glove box.
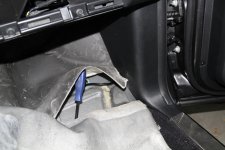
I oriented the air bag gauge at an angle to make it easier to see from the driver seat. I wanted to do the same with the tank gauge, but the back was ugly, and I thought it looked better straight in the middle. I still have half a glove box to use for registration papers if I fill up the lower glove box, or the two giant center console glove boxes.
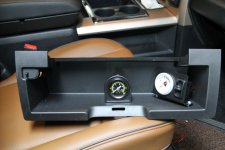
Here is how I plumbed and wired the gauges. I have a single line coming from the tank, it splits to feed the tank gauge and air inlet of the pneumatic switch. I placed the holes for the air lines so the gauges could be positioned as far back as possible. It made drilling and screwing the mounting holes a challenge. I replaced all the Tee fittings with compression fittings from Napa. I did't trust the push-in fittings.
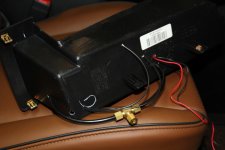
This silver bracket above the blue wire is what holds the upper glove box in place. You can see it by looking up through the lower glove box hole. I used a connector to ground the gauge lights to this bracket. I spliced dome light hot to the yellow wire on the glove box light plug.
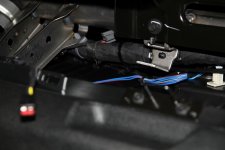
Just before buttoning it all up. All wires are connected and the gauges are plumbed. Even with all the excess air line, it fits together nicely. I had to wrestle the screws in from the air bag gauge over the lip. I didn't realize they were too long until after attaching the barbed fitting.
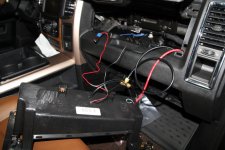
All put back together. I was impressed how solid the gauge and switch feel, despite being mounted to plastic. Even with the tank gauge straight, I have a clear view from the driver seat.
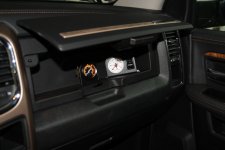
I made a bracket out of scrap steel to mount the air hose coupler to the bottom of the running board.
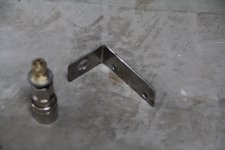
Here is the bracket mounted to the bottom of the running board. There are two screws holding the plastic caps on the end of the running boards. They make the perfect protected and invisible place to run the coupler. You cant see it unless you kneel down.
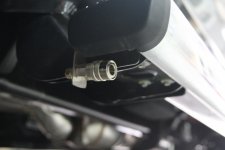
As far as wiring goes, my Ram has the upfitter switches. Thanks to the advice of others on the forum, I spliced the two positive leads on the pressure switch. Typically the switch is relay powered, triggered by an in-cab switch. I ran a lead from "Aux 3" on the upfitter switch. It is relay powered and protected by 25 amp fuse. I chose this one because it is "last known state" so if I shut the truck off with the switch on, it will be on when the truck restarts. I didn't pretty that wiring up yet since I'm waiting on a few parts. I'm adding an air solenoid to the drain so I can drain the tank from the cab. I'm also adding an air horn.
I ran out of time to install the airbags, but I have a functional, closed air system. Hopefully I'll get the bags in next weekend.
I picked up the Viair Constant Duty air system (part 10007) to use with airbags, and general airing up duty. I installed it this weekend in my 2014 Ram 3500. Hopefully my pictures can help the next person attempting this install.
I started by determining the best location for the tank and compressor. I found a spot on the passenger side, under the bed, between the duals and the running board.
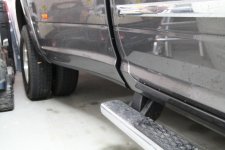
The front of the truck is to the left in this photo, I'm on my back, looking straight up. The forward rear spring hanger is just shadowed in this picture. This is the underside of the bed. There are two M12 x 1.75 threaded holes on frame of the bed. They are spaced about 19" apart.
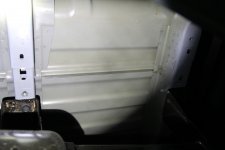
After measuring for the bolt holes, I test fit the plate. The plate measured 10" x 22" with a 3" square cut out of the corner to clear a frame member.
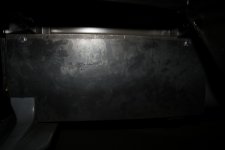
This is the orientation of the tank and compressor on the plate. Once mounted they hang upside down, with the tank on the outboard side.
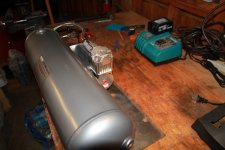
I lucked out with the remote air intake for the compressor. There was a hole already in the sheet metal, between the inner and outer bed skin. This photo is looking forward, inside the passenger side dual fender.
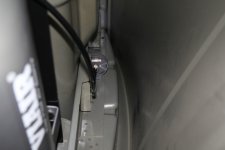
The scariest part of the install was ripping up the carpet and removing the glove boxes. The carpet pulls away easily from the outboard forward corner. It tucks back into place easily, too. I pulled the carpet far enough down to expose the bottom of the thick carpet pad. The lower glove box comes out easily, pull the sides in and tip it forward. There is a little spring loaded string that unhooks from the outboard side of the glove box. The upper glove box has a single screw holding it in on the back. Once removed the liner pops out by pushing it from the back. There are several clips around the perimeter holding it in place. One of these will pop as you push from behind. Unplug the light wire and it is all free.
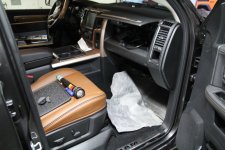
Once I had the carpet pad exposed, I lifted it to access the oval plastic cover. There are several of these covers, but this one is on the slanted portion of the passenger foot well. I wasn't sure how to get it off, but Al assured me it came off with a screwdriver. Sure enough, it pops up, and reveals a very nice hole for getting airlines into the cab. I routed the airlines behind the plastic panel to the right, and up behind the glove box.
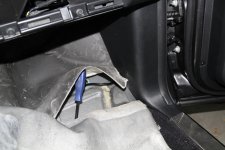
I oriented the air bag gauge at an angle to make it easier to see from the driver seat. I wanted to do the same with the tank gauge, but the back was ugly, and I thought it looked better straight in the middle. I still have half a glove box to use for registration papers if I fill up the lower glove box, or the two giant center console glove boxes.
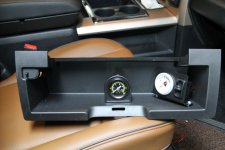
Here is how I plumbed and wired the gauges. I have a single line coming from the tank, it splits to feed the tank gauge and air inlet of the pneumatic switch. I placed the holes for the air lines so the gauges could be positioned as far back as possible. It made drilling and screwing the mounting holes a challenge. I replaced all the Tee fittings with compression fittings from Napa. I did't trust the push-in fittings.
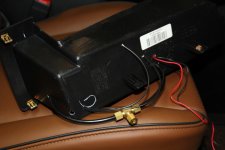
This silver bracket above the blue wire is what holds the upper glove box in place. You can see it by looking up through the lower glove box hole. I used a connector to ground the gauge lights to this bracket. I spliced dome light hot to the yellow wire on the glove box light plug.
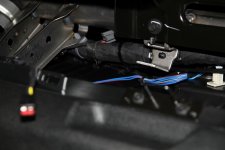
Just before buttoning it all up. All wires are connected and the gauges are plumbed. Even with all the excess air line, it fits together nicely. I had to wrestle the screws in from the air bag gauge over the lip. I didn't realize they were too long until after attaching the barbed fitting.
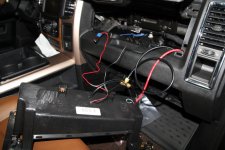
All put back together. I was impressed how solid the gauge and switch feel, despite being mounted to plastic. Even with the tank gauge straight, I have a clear view from the driver seat.
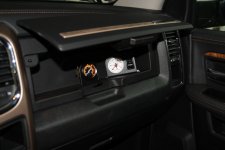
I made a bracket out of scrap steel to mount the air hose coupler to the bottom of the running board.
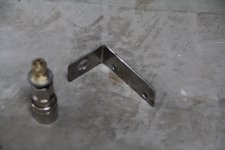
Here is the bracket mounted to the bottom of the running board. There are two screws holding the plastic caps on the end of the running boards. They make the perfect protected and invisible place to run the coupler. You cant see it unless you kneel down.
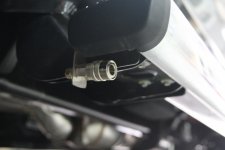
As far as wiring goes, my Ram has the upfitter switches. Thanks to the advice of others on the forum, I spliced the two positive leads on the pressure switch. Typically the switch is relay powered, triggered by an in-cab switch. I ran a lead from "Aux 3" on the upfitter switch. It is relay powered and protected by 25 amp fuse. I chose this one because it is "last known state" so if I shut the truck off with the switch on, it will be on when the truck restarts. I didn't pretty that wiring up yet since I'm waiting on a few parts. I'm adding an air solenoid to the drain so I can drain the tank from the cab. I'm also adding an air horn.
I ran out of time to install the airbags, but I have a functional, closed air system. Hopefully I'll get the bags in next weekend.